Services
Discover Our Process To Protect Your Workers
Site Inspection
A site inspection involves assessing the adequacy and compliance of safety measures designed to prevent falls at a workplace. If safety systems are already in place, inspectors check for proper installation, maintenance, and usage of equipment such as guardrails, harnesses, and safety nets. If safety systems are not in place, inspectors can asses what products should be added with custom design & installation.


Structural Review
A structural review involves evaluating the strength and integrity of the structures to which fall protection equipment is anchored. This process ensures that the structures can safely support the forces generated during a fall, thereby preventing equipment failure. The review is critical to verify that the fall protection systems are reliable and meet safety standards.
Roof Safety Analysis & Discussion
A roof safety analysis and discussion involves assessing the specific hazards and risks associated with working on a roof, such as edges, openings, and weather conditions. This analysis includes evaluating existing safety measures, like guardrails and anchor points, and determining if additional protections are needed. The discussion component involves collaborating with stakeholders to plan, implement, and ensure proper use of safety systems to prevent falls.


Safety System Conceptual Layout
A safety system conceptual layout involves creating a preliminary design that outlines the placement and arrangement of fall protection measures across a worksite. This layout includes identifying the locations for anchor points, guardrails, safety nets, and other critical components to ensure comprehensive coverage and worker safety. The conceptual layout serves as a blueprint for the detailed design and implementation of the fall protection system, aligning with safety standards and project requirements.
Engineered Design
An engineered design is a detailed, site-specific plan developed by qualified professionals to ensure that all safety measures, such as anchor points, lifelines, and guardrails, are structurally sound and meet regulatory requirements. This design takes into account the unique characteristics of the work environment, including load capacities and potential fall scenarios, to provide reliable and effective fall protection. The engineered design is critical for ensuring that the safety system functions correctly under real-world conditions, safeguarding workers from fall hazards.

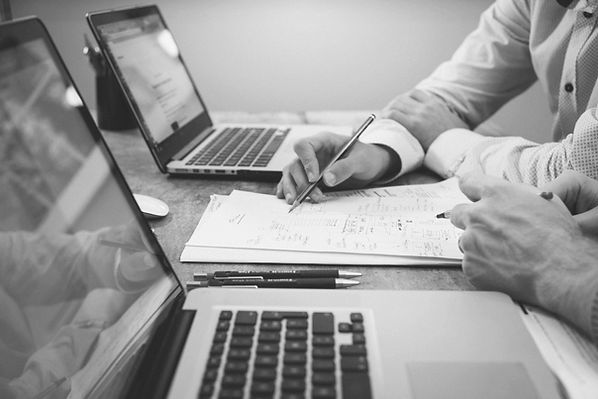
Proposal
A proposal involves a formal document that outlines the recommended safety solutions for preventing falls at a specific worksite. It includes details on the types of fall protection equipment, installation plans, compliance with safety regulations, and cost estimates. The proposal serves as a plan for implementing the fall protection system, ensuring that it meets the needs of the project and protects workers effectively.
Installation
Installation for fall protection safety systems involves the physical setup and integration of safety equipment, such as guardrails, anchor points, lifelines, and harnesses, according to a pre-approved design. This process requires skilled technicians to ensure that all components are securely installed and comply with safety standards and regulations. Proper installation is crucial for the system's effectiveness in preventing falls and ensuring the safety of workers at height.
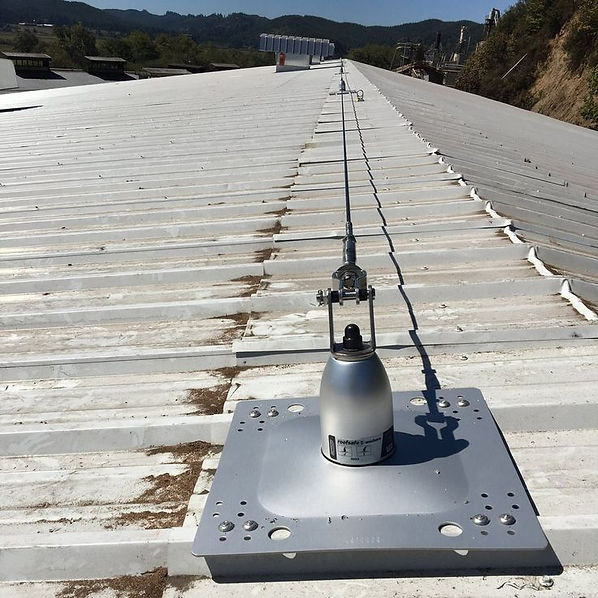

1 Year Inspection
A 1-year inspection is a mandatory and comprehensive review conducted annually to assess the condition and functionality of the installed safety equipment. Inspectors check for wear and tear, proper operation, and compliance with safety regulations, ensuring that all components remain effective and safe for continued use. This regular inspection is essential for identifying potential issues and maintaining the integrity of the fall protection system.
5/10 Year Load Testing
Depending on the anchor style, a mandatory 5/10 year load testing involves applying controlled loads to critical components, such as anchor points and lifelines, to verify their strength and ability to withstand the forces generated during a fall. This periodic testing ensures that the equipment remains structurally sound and compliant with safety standards over time. Conducted every 5 to 10 years, load testing is essential for detecting any degradation or weaknesses that could compromise the safety of the system.
